Wir wollen den Weg in die Industrie 4.0 gehen und stehen vor diesem Dilemma viel zu hoher Gemeinkostenzuschläge. Rahmenbedingungen, die wir nicht verändern können, sind die steuerlichen und finanzgesetzmäßigen Richtlinien. Wenn wir also keine Parallelrechnung – wie z.B. die Prozesskostenrechnung – aufmachen wollen, müssen wir auf dem Standardkostenrechnungssystem mit all seinen Fehlern aufsetzen. Wie also können wir dieses System, dessen Ziele hohe Transparenz, verlässliche Information zu jeder Zeit, schnelles Erkennen von Fehlentwicklungen sind und das darüber hinaus die Effekte des Lean Managements adaptiert, verbessern und optimieren, um es als Basis in einem modernen Unternehmen nutzen zu können? Es gibt dafür zwei Möglichkeiten.
Denkfehler Gemeinkostenzuschläge vermeiden
Zwei Ansatzpunkte zur Zielerreichung:
- Nutzen der Methoden des Lean Managements
- Etablieren eines Lean Cost Managements
Mit den Analysewerkzeugen des Lean Managements lassen sich die Kosten der Geschäftsprozesse und die indirekten Tätigkeiten verursachungsgerecht auf Produktgruppen zuordnen.
Auf Basis des Mengengerüstes lassen sich durch die Tätigkeitsstrukturanalyse und durch die Wertstromanalyse Prozesszeiten ermitteln, die eine genauere Zuordnung der bisher im Gemeinkostenblock untergegangenen Tätigkeiten auf Kostenträger stichpunktartig ermöglichen.
1.1 Die Tätigkeitsstrukturanalyse
Die Tätigkeitsstrukturanalyse liefert uns Aufschluss über Kerntätigkeit, Nebentätigkeit und organisatorische Tätigkeiten, wobei diese Tätigkeiten bezüglich ihres Charakters wertschöpfend, nicht wertschöpfend, aber notwendig und Verschwendung untersucht werden. Im indirekten Bereich gibt sie uns demnach Aufschluss darüber, was der Einzelne macht und wie viel Zeit er dafür benötigt. Hierdurch können wir ähnlich zur Produktion also feststellen, wie viel Kosten im administrativen Bereich für welche Prozesse, Produkte oder Produktgruppen anfallen.
1.2 Die Wertstromanalyse
Als zweiter Informationslieferant dient die Analyse der Wertströme. Durch ihre Darstellung können die Prozesse, die Schnittstellen, die Dauer der Prozesse, die Anzahl und Dauer von Rückfragen, die Bestände, die Kapazitäten und Prozesszeiten, die Warte- und Logistikzeiten sowie die wartungs-, störungs- und qualitätsbedingten Verlustzeiten dargestellt werden. Hierdurch ist es möglich, die Kosten quantitativ zu ermitteln und verursachungsgerecht zuzuordnen. In der Produktion wie auch in der Administration sowie in den indirekten Bereichen.
2. Das Lean-Cost-Management-Konzept
Dieses Konzept sattelt auf dem Standardkostenrechnungssystem auf, wie das Schema Abb. 2 zeigt, und ergänzt diese mit Informationen aus der Sicht des Lean Managements (siehe Abb. 1).
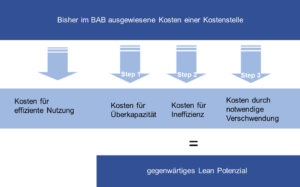
Es unterscheidet nach
- Kosten für die Wertschöpfung,
- Kosten für nicht wertschöpfende, aber notwendige Tätigkeiten (z. B. Transport),
- Kosten für ineffiziente Abläufe (z. B. Lagerkosten) und
- Kosten für Überkapazitäten (z. B. nicht ausgelastete Maschine).
Die Differenzierung dieser Kostentreiber erhöht die Kostentransparenz in Produktion und Administration und reduziert die Zuschlagssätze durch Gemeinkosten und Umlagen auf ein Minimum. Mit dem Werterfassungsbogen und Wertabrechnungsbogen wird der existierende Betriebsabrechnungsbogen ergänzt.
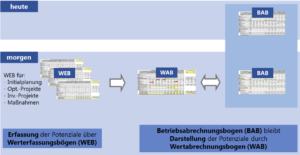
Dadurch zeigt er auch die Effekte der Optimierung durch die Lean-Management-Aktivitäten auf. Dies hilft, die Transparenz zu erhöhen und die Kostenzuordnung verursachungsgerecht durchzuführen.
Notwendiger Brush-up des Standardkostensystems
Erst mit den Informationen aus Untersuchungen und Analysen mithilfe der Lean Management-Methoden lassen sich zusammen mit dem ergänzten Betriebsabrechnungsbogen:
- Kosten sowohl der Produktion wie auch der Administration ohne hohe Gemeinkostenzuschläge oder Anlagen verursachungsgerecht zuordnen,
- Kosten, die nicht zum Wertschöpfungsprozess beitragen, identifizieren und gezielt reduzieren bzw. eliminieren,
- Kosten den Prozessen zuordnen und somit transparent darstellen,
- Effekte einer Lean-Initiative aufzeigen und greifbar machen.
Genau dies benötigen wir in der heutigen Zeit.
Bleiben Sie uns gewogen – bleiben Sie Lean.
Ihr Bodo Wiegand